Wprowadzenie
W dzisiejszej konkurencyjnej rzeczywistości gospodarczej, ograniczanie strat produkcyjnych i redukcja marnotrawstwa stają się kluczowymi elementami strategii przedsiębiorstw dążących do zwiększenia efektywności operacyjnej. Przyjęcie skutecznego systemu zarządzania produkcją, który pozwala na identyfikację i eliminację typowych strat, jest niezbędne dla firm, które chcą obniżyć koszty produkcji i jednocześnie podnieść poziom zadowolenia swoich klientów. W tym kontekście, lean manufacturing wyróżnia się jako metoda, która umożliwia osiągnięcie tych celów poprzez ciągłe doskonalenie procesów i eliminowanie wszelkiego rodzaju marnotrawstwa.
Rozumienie ograniczania strat produkcyjnych
Definicja i znaczenie ograniczania strat w produkcji
Ograniczanie strat produkcyjnych polega na systematycznym identyfikowaniu, analizowaniu i redukowaniu wszelkich aktywności, które nie dodają wartości do produktu końcowego, generując jednocześnie dodatkowe koszty. Takie podejście nie tylko przyczynia się do zwiększenia wydajności produkcji, ale także do ograniczenia kosztów operacyjnych.
Typowe straty w procesie produkcyjnym
Typowe straty obejmują nadprodukcję, nadmierne przetwarzanie, niepotrzebną obróbkę, straty związane z oczekiwaniem, zbędny transport oraz niewykorzystany potencjał pracowników. Każdy z tych rodzajów strat wymaga indywidualnej strategii redukcji w ramach systemu zarządzania produkcją.
Rodzaje strat: od nadprodukcji do niewykorzystanego potencjału
Nadprodukcja, będąca jednym z najbardziej kosztownych rodzajów strat, prowadzi do niepotrzebnego zwiększenia poziomu zapasów i związanych z nimi kosztów magazynowania. Ograniczanie strat energii i minimalizacja oczekiwania są kluczowe dla efektywnej produkcji, co wymaga skutecznego zarządzania procesami i ciągłego monitorowania wydajności produkcji.
Marnotrawstwo wg lean manufacturing
Podstawowe zasady lean manufacturing
Lean manufacturing, opierając się na swoich podstawowych zasadach, koncentruje się na eliminacji marnotrawstwa i ciągłym doskonaleniu procesów produkcyjnych. Narzędzia lean, takie jak Kaizen, SMED, Poka Yoke, 5S, a także TPM, są wykorzystywane do systematycznego ograniczania strat produkcyjnych i optymalizacji każdego etapu produkcji.
Narzędzia lean do ograniczania strat: Kaizen, TPM, SMED, Poka Yoke, 5S
Korzystając z narzędzi lean, takich jak Kaizen dla ciągłego doskonalenia, SMED do szybkiej wymiany narzędzi, Poka Yoke dla zapobiegania błędom, a także metodologii 5S dla organizacji miejsca pracy, przedsiębiorstwa mogą skutecznie redukować marnotrawstwo i zwiększać efektywność swoich operacji produkcyjnych.
Zobacz także: Aplikacja Audyt 5S
Lean manufacturing w Polsce: Przykłady i najistotniejsze zalety
W Polsce, lean manufacturing jest coraz częściej stosowane przez przedsiębiorstwa różnych branż jako sprawdzony sposób na ograniczenie kosztów produkcji i zwiększenie konkurencyjności. Przykłady firm, które z powodzeniem wdrożyły metody lean, pokazują, że dzięki tej filozofii możliwe jest nie tylko znaczące ograniczenie strat produkcyjnych, ale także poprawa jakości produktów i skrócenie czasu realizacji zamówień.
Czytaj więcej: 8 rodzajów marnotrawstwa.
Case Study w branży motoryzacyjnej
Przykład z branży motoryzacyjnej doskonale ilustruje, jak skuteczne ograniczanie strat produkcyjnych może przyczynić się do znaczącej redukcji marnotrawstwa. Firma XYZ, czołowy producent samochodów, zastosowała metodykę lean manufacturing, aby zmniejszyć nadprodukcję i zoptymalizować procesy w swoich zakładach. Dzięki wprowadzeniu systemu zarządzania produkcją opartego na koncepcji Kanban, udało się zredukować nadmierne zapasy o 30%, co bezpośrednio przekładało się na obniżenie kosztów produkcji. Kluczowym elementem strategii było zastosowanie narzędzia SMED, które pozwoliło na szybką zmianę ustawień maszyn, redukując czas przestoju i zwiększając wydajność produkcji. Implementacja 5S doprowadziła do lepszego zarządzania zapasami materiału i zmniejszenia strat miejsca w magazynach. Dzięki tym działaniom, XYZ osiągnęła lepsze wykorzystanie niewykorzystanego potencjału, co przełożyło się na wzrost konkurencyjności firmy na rynku.
Case Study w branży spożywczej
Innym przykładem efektywnego ograniczania strat produkcyjnych jest firma ABC, działająca w branży spożywczej. Skonfrontowana z problemem nadmiernego przetwarzania i wysokich odrzutów jakościowych, ABC zdecydowała się na wdrożenie zasad lean manufacturing. Wprowadzenie narzędzia Poka Yoke pozwoliło znacząco zmniejszyć liczbę wad jakościowych, poprawiając jednocześnie ogólną wydajność produkcji. Zastosowanie metodyki Kaizen umożliwiło zespołom produkcji na bieżąco identyfikować i eliminować przyczyny strat, takie jak zbędny transport czy nieefektywne zarządzanie procesami. Dzięki temu, ABC odnotowała znaczną redukcję marnotrawstwa, co w połączeniu z lepszym zarządzaniem zapasami, przyczyniło się do ograniczenia kosztów produkcji i poprawy satysfakcji klientów z jakości produktów.
POBIERZ KARTY PRACY — STRATEGIA NA A4!
- Pytania opracowane przez specjalistów
- Przykłady odpowiedzi z innych firm
- Pierwszy krok do rozpoczęcia świadomych działań w budowaniu strategii
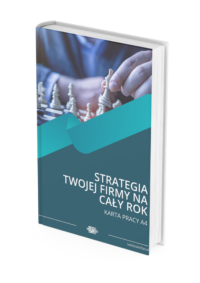
Podsumowanie i wnioski
Analizując powyższe case study oraz wcześniej przedstawione zagadnienia, można stwierdzić, że efektywne ograniczanie strat produkcyjnych wymaga zintegrowanego podejścia i zaangażowania na wszystkich poziomach organizacji. Lean manufacturing, dzięki swoim narzędziom, takim jak SMED, 5S, Poka Yoke, Kaizen, oraz zasadom zarządzania zapasami, oferuje sprawdzony sposób na redukcję marnotrawstwa i optymalizację kosztów produkcji.
Zalecenia dla przedsiębiorstw
W drodze do osiągnięcia lepszej efektywności operacyjnej i konkurencyjności na rynku, firmy powinny: Regularnie przeprowadzać audyty wewnętrzne, aby identyfikować obszary z potencjałem do redukcji strat produkcyjnych. Wdrażać i ciągle doskonalić system zarządzania produkcją z wykorzystaniem narzędzi i metodologii lean manufacturing. Szkolić pracowników w zakresie zasad lean manufacturing, aby zwiększyć ich zaangażowanie w proces ciągłego doskonalenia. Monitorować i analizować wpływ wprowadzonych zmian na ograniczenie kosztów produkcji i zwiększenie satysfakcji klientów.