Andon – klucz do szybkiego reagowania na problemy w produkcji
Co to jest Andon?
Andon to termin pochodzący z Toyota Production System, który odnosi się do wizualnego systemu sygnalizacji, znanego jako system Andon, służący do natychmiastowego informowania o problemach na liniach produkcyjnych. W przemyśle samochodowym, skąd Andon wziął swoje początki, był to system świateł, które operatorzy mogli uruchomić, aby sygnalizować problemy z jakością, brak materiałów, przestoje maszyn lub inne problemy zakłócające przepływ pracy na linii produkcyjnej.
Jak działa system Andon?
Głównym celem systemu Andon jest zapewnienie natychmiastowego powiadomienia o problemach, umożliwiając szybkie rozwiązanie problemu i minimalizację strat produkcyjnych. System Andon składa się zazwyczaj z zestawu kolorowych świateł, które są umieszczone w widocznym miejscu na linii produkcyjnej.
Na przykład, zielone światło może oznaczać normalne działanie, żółte – ostrzeżenie o potencjalnym problemie, a czerwone – krytyczny problem wymagający natychmiastowego zatrzymania produkcji. Operatorzy mogą uruchamiać te światła, aby zasygnalizować problem i wezwać pomoc. W niektórych bardziej zaawansowanych systemach Andon, operatorzy mogą także wprowadzać dodatkowe informacje o problemie, na przykład za pomocą panelu dotykowego lub skanera kodów kreskowych.
Przykładowe zastosowania systemu Andon
System Andon jest szeroko stosowany w wielu różnych branżach, każda z nich korzysta z niego w nieco inny sposób:
- Produkcja samochodów: W zakładzie produkującym części samochodowe, operatorzy mogą uruchamiać system Andon, gdy zauważą wadliwe części, brak materiałów lub awarię maszyny. Kiedy światła Andon zostaną włączone, zespół utrzymania ruchu, kierownicy produkcji lub inżynierowie jakości są natychmiast powiadamiani o problemie i mogą szybko podjąć odpowiednie działania.
- Produkcja elektroniki: W fabryce produkcji komponentów elektronicznych, Andon może być używany do sygnalizowania problemów z jakością, takich jak wadliwe komponenty, problemy z lutem czy problemy z montażem. W takim przypadku, Andon pomaga zespołom utrzymania ruchu, inżynierom jakości i operatorom linii w szybkim zidentyfikowaniu i rozwiązaniu problemu.
- Centra dystrybucji: W dużych centrach dystrybucji, systemy Andon mogą być wykorzystywane do sygnalizacji problemów związanych z logistyką, takich jak opóźnienia w dostawach, braki w magazynie czy problemy z wysyłką. Kiedy operatorzy zauważą problem, mogą uruchomić Andon, który natychmiast powiadamia menedżerów logistyki, umożliwiając szybkie rozwiązanie problemu.
Zalety korzystania z systemu Andon
Korzystanie z systemu Andon przynosi szereg korzyści. Przede wszystkim pozwala na szybsze wykrywanie i rozwiązywanie problemów na linii produkcyjnej, co prowadzi do mniejszych przestojów i wyższej jakości produktów. System Andon zwiększa zaangażowanie operatorów i kierowników w proces poprawy jakości, dając im narzędzia do komunikowania problemów i widzenia, jak ich działania wpływają na cały proces produkcyjny. Andon może pomóc w identyfikacji ukrytych problemów i wskazać obszary, które wymagają dalszej analizy i poprawy. Dzięki temu, system ten jest ważnym elementem kultury ciągłego doskonalenia, która jest kluczowym elementem skutecznego zarządzania produkcją w Toyota Production System.
Gdzie Andon może nie być odpowiednim narzędziem?
Andon może nie być odpowiednim narzędziem w firmach, gdzie produkcja nie jest zautomatyzowana lub linie produkcyjne są mało skomplikowane. W tego typu przedsiębiorstwach, w których procesy są prostsze i mniej podatne na różnego rodzaju problemy, wprowadzenie systemu Andon może być nieuzasadnione. Skala i koszty implementacji systemu Andon mogą przewyższać potencjalne korzyści, szczególnie jeśli nie ma dużych strat produkcyjnych związanych z przestojami czy jakością.
W takim przypadku, inne metody komunikacji i reagowania na problemy mogą być bardziej efektywne. Na przykład, małe firmy o niewielkiej skali produkcji mogą preferować bezpośrednią komunikację między pracownikami i kierownictwem, które mogą szybko zidentyfikować i rozwiązać problemy bez potrzeby skomplikowanego systemu wizualizacji.
Ważne jest, aby zawsze oceniać kontekst i specyfikę swojej firmy przed zdecydowaniem się na wdrożenie systemu Andon. Nie każda organizacja i każda linia produkcyjna będzie wymagała tego rodzaju rozwiązania. W niektórych przypadkach, prostsze i mniej kosztowne metody komunikacji i reagowania na problemy mogą być równie skuteczne, jeśli nie bardziej efektywne.
Wnioski
Andon, jako narzędzie wizualizacji problemów, stanowi ważny element Lean Management i Toyota Production System. Poprzez umożliwienie operatorom natychmiastowego powiadamiania o problemach na linii produkcyjnej, system ten pozwala organizacjom na szybkie reagowanie i minimalizowanie przestojów, co prowadzi do zwiększenia efektywności i rentowności.
Niezależnie od tego, czy jest to zatrzymanie linii produkcyjnej, aby zapobiec wadliwym produktom, czy skierowanie uwagi kierowników na problem z jakością, system Andon pomaga zidentyfikować problem i podjąć działania w celu zapobiegania powtarzaniu się problemu w przyszłości. Andon to ważny krok na drodze do Lean Manufacturing i doskonałości produkcyjnej.
ODBIERZ DARMOWĄ CHECKLISTĘ PREZESA FIRMY PRODUKCYJNEJ
Zyskasz kontrolę nad swoim czasem — oszczędzisz mnóstwo czasu i ustalisz priorytety!
Zidentyfikujesz obszary do usprawnienia – 99% prezesów korzystających z checklisty już je znalazło!
Skontrolujesz wydatki i przygotujesz się do kolejnych inwestycji.
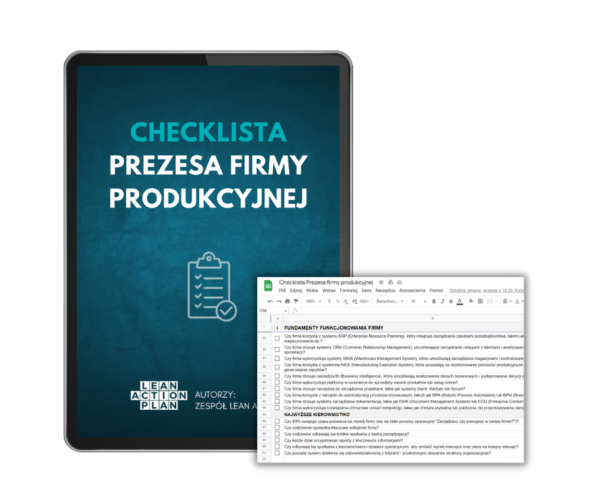