Czym jest mapowanie procesów i dlaczego jest niezbędne?
Mapowanie procesów to technika, która pozwala dokładnie zrozumieć, jak działają procesy w organizacji. Obejmuje tworzenie wizualnych diagramów przedstawiających kroki, osoby odpowiedzialne i zasoby potrzebne do osiągnięcia celu. Może dotyczyć różnych obszarów: produkcji, logistyki, administracji, a nawet obsługi klienta.
Dzięki mapowaniu procesów firmy zyskują:
- Przejrzystość w działaniach,
- Identyfikację wąskich gardeł,
- Ułatwienie współpracy między działami,
- Możliwość eliminacji zbędnych kroków i redukcji kosztów.
Przykład: W jednej z firm e-commerce mapowanie procesów logistycznych ujawniło, że najwięcej opóźnień wynika z nieefektywnego przepływu informacji między działem sprzedaży a magazynem. Poprzez wdrożenie szczegółowej mapy procesu firma skróciła czas realizacji zamówień o 18%.
Czym są problemy systemowe i jak wpływają na popełnianie błędów przez pracowników?
Problemy systemowe wynikają z błędów organizacyjnych, proceduralnych lub technicznych, które mogą sprawić, że pracownik popełniający błąd nie zawsze jest jedynym odpowiedzialnym za pomyłkę. Przykładem mogą być niejasne procedury, niewłaściwe narzędzia, a nawet nieadekwatne zarządzanie czasem pracy i zasobami ludzkimi. W efekcie pracownik popełniający błąd staje się raczej ofiarą niedoskonałości systemu niż wynikiem własnych działań. Z tego względu często konieczne jest nie tylko naprawianie błędu pracownika, ale także rozwiązywanie problemów leżących u jego źródła.
1. Brak jasno określonych celów mapowania procesów
Rozpoczęcie mapowania bez wyznaczonego celu jest jednym z głównych błędów. Często firmy tworzą schematy procesów „na wszelki wypadek”, bez sprecyzowania, co chcą osiągnąć. Bez celu mapa staje się jedynie estetycznym dokumentem, a nie narzędziem poprawy wydajności.
Jak wyznaczyć cel?
- Zidentyfikuj problem: Czy celem jest redukcja czasu realizacji, poprawa jakości, czy eliminacja błędów?
- Określ miary sukcesu: Skrócenie czasu o 15%, zmniejszenie kosztów o 10%.
- Dobierz narzędzia: Stosuj diagram SIPOC do analizy wejść i wyjść lub mapę strumienia wartości (VSM).
Przykład z firmy produkcyjnej: Firma z branży automotive miała problem z opóźnieniami na etapie montażu. Mapowanie procesu produkcji ujawniło, że dostawy podzespołów są nieefektywne. Wdrożenie mapy swimlane poprawiło komunikację między dostawcami a działem planowania.
2. Tworzenie zbyt ogólnikowych map procesów
Mapowanie procesów ułatwia analizę działań tylko wtedy, gdy mapa jest szczegółowa. Ogólnikowe mapy, które pomijają detale, prowadzą do błędnych wniosków i nie pozwalają dostrzec wąskich gardeł w procesie.
Jak stworzyć szczegółową mapę procesu?
- Rozbij proces na etapy: Każdy krok musi zawierać informacje o czasie, odpowiedzialności i zasobach.
- Stosuj narzędzia:
- LucidChart do tworzenia precyzyjnych map,
- Microsoft Visio do zaawansowanych diagramów przepływu procesu.
- Uzupełnij mapę danymi: Uwzględnij dane kroków procesu oraz zależności między nimi.
Przykład: Firma logistyczna odkryła, że 12% czasu pracy magazynierów było marnowane na poszukiwanie towarów. Szczegółowe mapowanie procesów magazynowych pozwoliło zidentyfikować problem z oznaczeniami półek i zoptymalizować układ przestrzeni.
3. Korzystanie z niewłaściwych narzędzi mapowania procesów
Bez odpowiednich narzędzi mapowanie procesów jest nieefektywne. Firmy, które używają arkuszy kalkulacyjnych lub ręcznie rysowanych diagramów, tracą czas i dokładność.
Jakie narzędzia warto wybrać?
- LucidChart – intuicyjne narzędzie online do mapowania procesów współpracy.
- Microsoft Visio – idealne do tworzenia zaawansowanych szczegółowych map procesów.
- Miro – doskonałe do pracy zespołowej i wizualnego mapowania procesów.
- DRAW.IO – darmowa platforma do szybkiego tworzenia diagramów.
Przykład: Firma logistyczna, która wcześniej używała ręcznych rysunków, przeszła na Microsoft Visio i stworzyła szczegółową mapę strumienia wartości. Analiza pozwoliła obniżyć koszty transportu o 10%.
4. Ignorowanie procesów współpracy między działami
Mapowanie procesów współpracy jest kluczowe dla organizacji, gdzie zespoły muszą ze sobą współpracować. Brak tego elementu prowadzi do chaosu, opóźnień i konfliktów między działami.
Jak poprawić współpracę?
- Twórz mapy swimlane, które pokazują odpowiedzialność poszczególnych zespołów.
- Używaj matrycy RACI, aby przypisać role i obowiązki.
- Stosuj diagram SIPOC, aby precyzyjnie określić wejścia i wyjścia procesu.
Przykład: W firmie technologicznej mapowanie procesów współpracy między działem IT a marketingiem ujawniło, że opóźnienia wynikają z braku zatwierdzeń. Poprawa procesu skróciła czas wdrożenia kampanii o 40%.
5. Brak wdrożenia i aktualizacji wyników mapowania procesów
Stworzenie mapy to dopiero początek. Firmy często popełniają błąd, nie wdrażając wyników mapowania lub nie aktualizując schematów wraz ze zmianami w organizacji.
Jak wdrożyć wyniki mapowania?
- Analizuj rezultaty: Monitoruj zmiany i sprawdzaj, czy przynoszą oczekiwane efekty.
- Regularnie aktualizuj mapy: Procesy ewoluują, więc procedury mapowania procesów muszą być na bieżąco dostosowywane.
- Zastosuj metodę VSM: Monitorowanie mapy strumienia wartości ułatwia ciągłą optymalizację.
Przykład: Firma usługowa wdrożyła szczegółową mapę procesu dla działu obsługi klienta. Regularna aktualizacja pozwoliła skrócić czas reakcji na zgłoszenia o 50%.
Case Study 1: Optymalizacja procesów produkcyjnych w firmie przemysłowej
Firma z branży przemysłowej zauważyła, że realizacja zamówień trwała znacznie dłużej niż zakładano. Proces produkcji składał się z wielu etapów, jednak brakowało przejrzystości co do odpowiedzialności i kolejności działań. W wyniku tego:
- Pracownicy tracili czas na zbędne czynności,
- Zasoby były nieefektywnie wykorzystywane,
- Występowały regularne opóźnienia w dostawie gotowych produktów.
Rozwiązanie:
Zastosowano mapowanie procesów produkcji z użyciem:
- Mapy swimlane – pozwoliło to przypisać odpowiedzialność do poszczególnych działów i osób.
- Diagramu SIPOC – dokładnie zidentyfikowano dostawców, wejścia, procesy, wyjścia i odbiorców.
- Mapy strumienia wartości (VSM) – ujawniono, że 18% czasu procesu było tracone na oczekiwanie na podzespoły.
Efekty:
Po wdrożeniu zmian:
- Skrócono czas produkcji o 20%,
- Zoptymalizowano zarządzanie materiałami, co zmniejszyło koszty magazynowania,
- Zwiększono terminowość dostaw do klientów.
Case Study 2: Poprawa obsługi klienta w firmie e-commerce
Firma e-commerce zauważyła rosnącą liczbę skarg na opóźnienia w realizacji zamówień. Problem wynikał z braku synchronizacji między działem sprzedaży, magazynem a logistyką. Proces był chaotyczny, a dane nie były odpowiednio przekazywane.
Rozwiązanie:
Przeprowadzono mapowanie procesów współpracy między działami, wykorzystując:
- Diagram przepływu procesu – wizualizacja pokazała, gdzie informacje „giną” w komunikacji,
- Matrycę RACI – wyznaczono role i odpowiedzialności każdej osoby w procesie,
- Mapę swimlane – stworzono przejrzystą strukturę przepływu pracy między działami.
Efekty:
- Skrócono czas realizacji zamówień o 25%,
- Wyeliminowano błędy wynikające z braku komunikacji,
- Zwiększono poziom satysfakcji klientów o 40%.
Dzięki mapowaniu procesów firma zyskała lepszą organizację pracy, co przełożyło się na większą efektywność i mniejsze koszty operacyjne.
Podsumowanie: Dlaczego warto mapować procesy?
Korzyści mapowania procesów to m.in.:
- Identyfikacja i eliminacja wąskich gardeł,
- Poprawa współpracy między działami,
- Skrócenie czasu pracy i redukcja kosztów,
- Lepsze zarządzanie zasobami.
Przydatne linki:
Mapowanie procesów umożliwia firmom osiąganie wyższej efektywności operacyjnej. Warto wdrażać je regularnie i unikać kluczowych błędów!
POBIERZ KARTY PRACY — STRATEGIA NA A4!
- Pytania opracowane przez specjalistów
- Przykłady odpowiedzi z innych firm
- Pierwszy krok do rozpoczęcia świadomych działań w budowaniu strategii
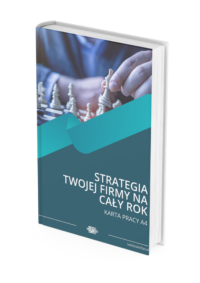